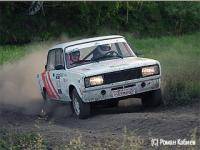
Попробуем сюда выкладывать полезные сведения о машинках, изложенные доступным языком, которые помогут в освоение машинки и начнем с любимой педальки начинающих: сцепление!
Только зарегистрированные и авторизованные пользователи могут оставлять комментарии.
ЗАДАЧИ АММОРТИЗАТОРОВ
Амортизаторы появились на автомобилях задолго до широкого внедрения известных сегодня цилиндрических конструкций с перемещающимся поршнем. Первоначально почти повсеместно распространенные рессоры совмещали в себе одновременно и пружину и амортизатор. Пружинили листы, они же и терлись друг об друга, стянутые для этого в пакеты, переводя кинетическую энергию в тепловую и гася вертикальные колебания. Идея разделить функции пружин и демпфирующих устройств была вынужденной. Широкое внедрение независимой подвески, значительно повышающей комфорт и управляемость, подвело к этому чисто конструктивно. С приходом винтовых пружин вместо рессор рядом с ними так и просилось что-нибудь цилиндрическое. К тому же, разболтанную рессору приходилось менять целиком или перетягивать, что по трудоемкости значительно превосходило замену пары амортизаторов, закрепленных двумя гайками каждый. Механическое трение заменили на гидравлическое. Первое было очень трудно контролировать, по мере быстрого износа трущихся поверхностей характеристики всей системы так же быстро менялись. Кроме того, все это сопровождалось, обычно, скрежетом и скрипом что, как Вы понимаете, не добавляло комфорта пассажирам. Гидравлическая система с маслом, прогоняемым через тонкие калиброванные отверстия клапанов служила на несколько порядков дольше, не меняя существенно своих характеристик. К тому же появилась возможность достаточно четко дозировать эти характеристики, простой сменой двух или четырех амортизаторов делать один и тот же автомобиль более комфортабельным или более спортивным. Гидравлическое трение имело перед механическим еще одно бесспорное преимущество. Клапаны, через которые протекает масло, можно настроить так, что сопротивление амортизатора будет разным в зависимости от направления работы подвески. Обычные амортизаторы имеют усилие при отбое в два-четыре раза больше, чем усилие при сжатии. Это означает, что когда колесо наезжает на препятствие, оно с легкостью идет вверх, а затем, уже при возврате его назад, пружинам и приходится работать, тратя накопившуюся при сжатии кинетическую энергию. Меняя характеристики сопротивления ходов, получают "более спортивные" или "более комфортные" подвески, не меняя принципиально их конструкции.
КОНСТРУКЦИИ АММОРТИЗАТОРОВ
Все амортизаторы принято делить на "гидравлические", "газовые" и "поддутые" ( c газом низкого давления). Деление это условно потому, что во всех трех случаях "центральный" узел - клапан остается принципиально неизменным и во всех трех случаях в качестве компенсационного элемента используется газ. Центральный клапан перемещается в центральном цилиндре и отличия начинаются дальше. Гидравлические амортизаторы и поддутые имеют еще и внешний цилиндр, куда перетекает масло через систему нижнего клапана. Газовый амортизатор внешнего цилиндра не имеет и вся его конструкция упакована в одном. (СМ. РИС. http://vkontakte.ru/photos.php?act=show&id=-8221...)
Таким образом, амортизаторы логичнее делить на двухтрубные и однотрубные. При работе любых амортизаторов, по определению, выделяется большое количество тепла, поэтому от применяемого в них масла требуется не только коррозионная, но и термическая стойкость - способность выдерживать температуры до 160 градусов не меняя структуры и свойств. Одновременно с этим актуальна задача отвода тепла. Двухтрубные гидравлические амортизаторы отводят тепло хуже чем однотрубные высокого давления, ведь у первых "генератор тепла" - центральный цилиндр закрыт сверху еще одним соосным цилиндром, наполненным маслом и компенсационным газом. Зачем нужен компенсационный объем газа? Жидкость, как известно, не сжимается. Вернее, сжимается, но очень незначительно. Поэтому, если бы не было компенсационного объема, поршень внутри цилиндра при резком перемещении (типа удар) натыкался на "каменную стену" масла, которое в силу своей большой инерции еще не начало течь через калиброванные отверстия клапанов. Именно компенсационный объем газа сжимается первым и принимает на себя удар и лишь потом масло начинает проходить через калиброванные отверстия клапанов центрального штока. К тому же при работе масло нагревается, часто до значительных температур. Увеличение его объема при этом необходимо компенсировать и делает это небольшая порция газа.
Гидравлические амортизаторы (СМ. РИС. http://vkontakte.ru/photos.php?act=show&id=-8221... ) демпфируют мягче потому, что у них две системы клапанов, в отличие от однотрубных газовых, у которых только одна, расположенная на штоке, плюс газ у них под более низким давлением. Вместе с этим, они максимально инертны, медленно реагируют на перемещения колеса, особенно при низкочастотных колебаниях небольшой амплитуды. Чем выше давление газа, подпирающего масло, тем выше "быстрота реакции" амортизатора. В амортизаторах высокого давления и масло и газ расположены последовательно в одном цилиндре и разделены плавающим клапаном. Газ (обычно это азот) находится под давлением около 25 атмосфер. Таким образом, клапан штока находится все время в "поджатом", "подпружиненном" состоянии и гораздо быстрее реагирует на выбоины и ухабы дороги. Гидравлические двухтрубные амортизаторы имеют еще несколько особенностей, становящихся недостатками при определенных режимах эксплуатации автомобиля. При резком перемещении поршня на обратной стороне клапана создается разряжение и могут образоваться кавитационные пузырьки. Это резко изменяет характеристики демпфирования. При часто повторяющихся резких перемещениях, например, при прохождении раллийной трассы, амортизатор просто "вскипает" - кавитационные пузырьки и газ компенсационного объема смешиваются с маслом в подобие эмульсии, при этом демпфирование практически исчезнет.
Газонаполненные амортизаторы высокого давления появились, в основном, как ответ на необходимость решения этой проблемы. Подпружиненное масло практически не вспенивается, а отделение компенсационного объема плавающим поршнем снимает вопрос о возможном смешивании газа с маслом. Именно поэтому амортизаторы высокого давления можно переворачивать "вниз головой", например в стойках Макферсона, а гидравлические - нет. Двухтрубные амортизаторы тяжелее однотрубных. Установка первых на автомобиле ведет к увеличению неподрессоренной массы подвески и, как следствие, увеличению ее инертности. При частых перемещениях вверх-вниз на характерных участках дороги (типа раллийная трасса), инерция заставляет подвеску как бы "задумываться" поочередно то в верхней, то в нижней точки и пропускать очередное летящее на нее препятствие или яму. В этом заключается еще одна причина всеобщей любви спортсменов к однотрубным газонаполненным амортизаторам.
Исправные и неисправные амортизаторы
Автомобиль, колесо которого вывешено в воздухе, не может тормозить, разгоняться или поворачивать, т.е. становится неуправляемым. Пружины стремятся вернуть колесо на землю, но ударившись о покрытие, оно так же быстро отскакивает назад. Колебания повторяются, автомобиль встречает новые препятствия и ямы и, если бы не амортизаторы, при скоростях больше 20-30 км/час управлять им становится практически невозможно. Характеристики же исправного амортизатора рассчитаны так, что колесо делает только одно "полноценное" движение вверх, возвращается вниз и после этого 80% энергии удара погашено амортизатором - превращено в тепло и рассеяно в воздухе. Исправные амортизаторы являются ведущим элементом активной безопасности. Опасность ситуации заключается в том, что, во-первых, водители этого не осознают, а во-вторых износ амортизаторов происходит постепенно, часто без видимых или слышимых признаков. Водитель привыкает к "новому" поведению автомобиля, но в тот момент, когда нужно будет перестроиться и уйти от неожиданно появившегося встречного автомобиля или поворот окажется круче, чем он выглядел при входе в него... Виноваты будут не амортизаторы, а водитель, не справившийся с управлением. Чем более неисправны амортизаторы, тем больше времени колесо проводит в воздухе, а не в контакте с дорогой. В результате увеличивается тормозной путь, особенно нагруженного автомобиля и с прицепом, снижается скорость безопасного прохождения поворотов и порог начала аквапланирования, происходит интенсивный износ шин, узлов ходовой части, ухудшается освещение дороги и происходит ослепление встречных водителей. Особенно не любят неисправные амортизаторы системы АБС, ПБС и Traction Control. Их датчики настроены на отслеживание поведения колес, катящихся по земле, а не вращающихся со страшной силой в воздухе. Электронные "мозги" этих систем путаются и дают неверные указания исполнительным механизмам. Самое же главное, ухудшается управляемость, автомобиль начинает рыскать, особенно при изменении скорости (разгоне или торможении). Самое же последнее, но то, что принято замечать сразу - значительно снижается комфортность поездки, машину трясет, вибрация становится неравномерной и часто сопровождается стуками. Это первый очевидный признак неисправности амортизаторов. Значит, пришло время для их осмотра и диагностики.
Диагностика амортизаторов
Выделяют четыре способа диагностики амортизаторов - от самого поверхностного до "глубинного" с применением, конечно же, микропроцессоров и компьютеров.
1. Визуальный осмотр
Несмотря на то, что амортизатор как будто специально расположен в самом неудобном для осмотра месте, этот тест один из самых достоверных и, несомненно, дешевых и оперативных. На амортизаторе может быть заметен масляный "туман", но не должно быть подтеков. Подтеки масла свидетельствуют о потере герметичности и о том, что амортизатор уже "кончен" или недалек от этого. Если при проверке у Вас возникли сомнения, протрите амортизатор насухо и осмотрите его через несколько дней работы. Обратите внимание на состояние буфера отбоя и пыльника. Масло, попавшее на их поверхность не только говорит о проблемах амортизатора, но и приводит к их очень быстрому разрушению. Это еще более ускорит выход из строя всего амортизатора - своеобразный эффект снежного кома. Важнейшим элементом визуального осмотра является состояние шин. Если на их поверхности, особенно по боковой кромке наблюдаются неравномерные пятна износа, это явный знак неисправности амортизаторов. Можно также наблюдать за поведением колеса при движении из другого автомобиля. Здесь не нужно быть экспертом, чтобы заметить, если оно "скачет" и что амортизатор неисправен. Еще одним "визуальным" тестом является осмотр штока. Визуальным в кавычках потому, что в отличие от всего сказанного выше амортизатор нужно снимать. Тем не менее, если на полированной поверхности вы обнаружили следы от зажимов или пятна ржавчины - меняйте амортизатор. Другим печальным сигналом может быть износ хромового покрытия в виде пятна с одной стороны. Это следствие неправильной затяжки при установке, приведшей к несоосности цилиндра и штока. Результатом также будет потеря герметичности и выход амортизатора из строя.
2. Тест на "покачивание"
Самый известный и самый критикуемый тест. Действительно, раскачав автомобиль за угол и отпустив его в нижней точке, можно выявить только заведомо "убитый" амортизатор. С ним автомобиль будет продолжать колебания. Однако, если он встал "как вкопанный", это может означать совсем не работающий, а наоборот, заклинивший амортизатор. Делайте этот тест больше для самоуспокоения и старайтесь "поймать" момент начала потери рабочих свойств при движении.
3. Оценка управляемости автомобиля в движении
Комфорт в автомобиле при его движении понятие гораздо более субъективное, чем устойчивость и управляемость. Неисправные амортизаторы приводят к тому, что на скоростях начиная с 80 километров в час автомобиль начинает рыскать, особенно при встрече с мелкими неровностями дороги. Снижается курсовая устойчивость, начинается продольная и поперечная раскачка. Раскачка имеет продолжительный незатухающий характер. При движении по неровностям автомобиль показывает замедленную реакцию на руль - тот уже вывернут, а машина все не начинает поворачивать. Повторяясь, можно сказать, что водитель постепенно привыкает к отклонениям в управляемости автомобиля и на первых порах подстраивается под них. Действительно разницу можно оценить только сравнив два автомобиля - один с новыми, а другой - с "убитыми" амортизаторами. Однако, такая ситуация больше характерна для полигонов и журнальных статей, чем для реальной жизни. Поэтому, при первых подозрениях на проблемы с управляемостью и устойчивостью следует покачать автомобиль за углы, осмотреть амортизаторы и, либо немедленно менять их на новые (при наличие течи масла), либо отправляться на специализированный пункт инструментального контроля.
4. Инструментальный контроль (стендовая диагностика)
Различают вибрационные стенды и проверку демпфирующего усилия на испытательных стендах. В первом случае Вам необходимо заехать на автомобиле на площадку исполнительного механизма стенда и за несколько минут на нем будет получена диаграмма осевых колебаний. Сравнивая ее со специфичными граничными характеристиками для данного автомобиля, специалисты станции могут практически безошибочно оценить состояние амортизаторов. Проверка демпфирующего усилия требует разборки подвески и снятия амортизатора. Такая диагностика позволяет получить максимально точную информацию, но дорога и сложна уже сама по себе. Просто оцените стоимость снятия и установки амортизаторов. Стендовая оценка демпфирующего усилия оправдана только в том случае, если есть сомнения в поведении дорогих амортизаторов стоимостью от ста долларов и в результате может отпасть необходимость их замены.
От чего умирают амортизаторы
В самом амортизаторе сломаться могут только две вещи - выйти из строя клапаны и нарушиться герметичность сальника штока. Если поломка первого рода встречается достаточно редко, то вторая является основной и имеет множество причин для происхождения. Надежно работающий сальник амортизатора представляет собой достаточно нетривиальную конструкторскую задачу. Действительно, его шток проходит через масляную ванну изнутри наружу, повторяя это циклическое движение сотни тысяч раз, часто со значительными ускорениями, нагреваясь (и расширяясь), вместе с нагревающимся при работе маслом. Еще сложнее ситуация у однотрубных систем, ведь там все усугубляет давление газа, которое равномерно распространяется и на масло, по определению стараясь вытолкнуть его наружу. После решения конструкторской задачи на первое место выходит качество изготовления и качество материалов. Не менее важны и показатели стабильности производства и тех допусков, посадок и отклонений, которые закладываются в каждый амортизатор. Все это и входит в определение такого емкого слова как "культура производства". Именно поэтому одни амортизаторы служат дольше чем автомобиль, а другие нужно проверять каждые 20 тысяч километров. Но и в цене разница может доходить до 10 раз. Во время работы на автомобиле шток амортизатора "собирает" взвешенную в воздухе пыль и иные механически (абразивно) и химически агрессивные вещества типа соляного раствора, которым поливают зимой наши дороги. Они просачиваются в небольших количествах даже через исправный защитный кожух (пыльник). Другое дело, когда этот кожух поврежден или даже частично разрушен. Пыль и грязь, попадая на шток, как наждаком срезают поверхность сальника и масло начинает просачиваться наружу. Полированная поверхность штока рассчитана на многолетнюю эксплуатацию. Появляющаяся на ней ржавчина свидетельствует либо о сверхагрессивной среде, либо о проблемах с подбором материала и соблюдением качества производства его изготовителем. Раковинки ржавчины вызывают интенсивный износ сальника, но самое обидное, когда шток поврежден еще при установке горе-мастером, использовавшем в работе пассатижи, струбцины или иные металлические захваты. Царапины на полированной поверхности очень скоро приведут к разрушению сальника. Для избежания же неравномерного износа поверхности штока затягивать амортизатор до упора нужно только когда автомобиль стоит на колесах с нормальной нагрузкой. Простая регулярная проверка целости и сохранности пыльника и правильная первоначальная установка амортизатора смогут значительно продлить его жизнь. Труднее избежать неблагоприятных режимов работы, изнашивающих внутренние клапаны. К таким относятся предельно высокие и низкие температуры и длительная езда на невысокой скорости с большими амплитудами перемещения штока. Действительно, зиму, лето и дачные участки с "бетонками" не отменишь, но вот буфер отбоя нужно также проверять регулярно. Он размягчается от попадающего на него масла и при его разрушении подвеску может "пробить".
Выбор амортизаторов
Замена амортизаторов, по сравнению, скажем, с заменой масла или топливного фильтра, может привести к значительным изменениям в поведении автомобиля. Отличаются не только "гидравлика" и "газ", но и однотипные амортизаторы различных фирм. Комфорт и управляемость - показатели технически противоположные. Увеличивая один из них, мы уменьшаем другой и так далее. Неверно также утверждать, что газовые одноцилиндровые амортизаторы "в целом" лучше гидравлических двухтрубных. Да, они легче, лучше охлаждаются, практически не вспениваются и их можно переворачивать "вверх головой". Однако, все эти свойства становятся реальными преимуществами только в условиях спортивных соревнований. Для подавляющего числа "рядовых" автомобилистов и условий их езды гидравлические амортизаторы справляются со своими задачами на сто процентов. Более того, большинство из тех, кто попробовал, отмечает излишнюю жесткость газовых однотрубников. То же самое относится и к ценовому подходу. Практически все однотрубные газонаполенные амортизаторы на 30-50% дороже гидравлических. То же самое относится и к соотношению цен на амортизаторы отечественного и зарубежного производства, но разница здесь измеряется уже "разами". Стоит ли поэтому ломать копья и экспериментировать?
Пяти-десятилетняя иномарка вполне пройдет еще два-три года на новой гидравлике средней цены, а подержанный отечественный автомобиль и вовсе опасно ставить на "газ". Его кузов наверняка уже начал терять и без того небольшую изначальную жесткость и даже год, проведенный на газонаполненных амортизаторах, разобьет его окончательно. Для амортизаторов, как и для всех расходных материалов, справедливо следующее правило - чем более раскручена марка, чем больше денег вкладывает фирма в рекламу, тем чаще их подделывают и тем больше вероятность наткнуться на продукцию третьих-четвертых стран в красивой упаковке. Точно также, как и производители фильтров и сцеплений, амортизаторные компании делятся на "больше" поставщиков конвейеров и тех, кто ориентируется на розницу. Точно также, как и в случае с ВАЗом предпочтение при замене стоит отдавать "родным" амортизаторам, для иномарок существуют "оригинальные" поставщики. На рынке сегодня представлены все основные производители. Их условно можно разбить на три группы, начиная с самых дорогих, но гарантированно надежных и заканчивая массовыми и доступными моделями: 1. Koni, Bilstein, de Carbon (только французский, а не алжирский). 2. Boge, Sachs, KYB. 3. Monroe, Delco, QH, Rancho, Gabriel.
При покупке амортизатора тщательно сверьте комплектность набора с тем, что значится в каталоге. В него могут входить специальные детали крепления, буферы отбоя, пыльники и т.д. При установке нельзя перетягивать резиновые втулки крепления, а окончательную затяжку следует производить на стоящем на колесах автомобиле с тем, чтобы обеспечить со-осность элементов амортизатора.
Последнее замечание
Меняйте амортизаторы на СТО. Если у Вас нет достаточного опыта и специального инструмента не стоит экспериментировать. Специальный инструмент (съемник) требуется на многих моделях автомобилей (а на многих - не требуется) для сжатия и фиксации пружины подвески для ее снятия. При неумелом обращении, последняя может в буквальном смысле слова "выстрелить", последствия чего разрушительны и даже убийственны.
Колесные диски делятся на две большие группы: стальные и сделанные из легких сплавов.
СТАЛЬНЫЕ ДИСКИ
Стальные диски, точнее, их части, штампуют из листа, а потом эти части соединяют сваркой. Получается предельно дешево и достаточно качественно — именно поэтому подавляющее большинство автомобилей на заводском конвейере оснащают стальными.
Достоинства:
- невысокая цена;
- довольно высокая прочность и возможность восстановления даже в случае очень сильного смятия закраин.
Основные недостатки:
- большая масса,
- невысокая точность изготовления (а значит, возможны проблемы с балансировкой) и устаревший дизайн.
- невысокая коррозионная стойкость, во многом обусловленная качеством покрытия. При этом самая низкая коррозионная стойкость у дисков, покрытых эмалью и электрофорезом.
ЛЕГКОСПЛАВНЫЕ ДИСКИ
Легкосплавные диски по многим свойствам лучше стальных. Они допускают любые игры с дизайном, у них высочайшая точность изготовления, они прекрасно отводят тепло от тормозного узла, но главное — они легкие (чем легче диски, тем меньше общая масса неподрессоренных частей автомобиля, а значит, тем лучше). Это общие достоинства. Уточненно же судить об их плюсах и минусах можно, лишь учитывая, каким способом и из какого именно сплава они сделаны — тут много нюансов, колесо колесу рознь.
По способу изготовления легкосплавные диски делятся на литые и кованые.
Литые диски
Литой диск имеет зернистую внутреннюю структуру металла, и в этом его основной минус: при долгой езде по колдобинам в металле идет процесс накопления микротрещин (невидимых и потому опасных), которые рано или поздно проявят себя- от сильного удара диск может расколоться. Недостатки:
- литой диск требует серьезной защиты поверхности, без этого он быстро покрывается белесой оксидной пленкой и теряет товарный вид.
- он довольно хрупкий; при очень сильном ударе раскалывается, что на высокой скорости чрезвычайно опасно. Чтобы обеспечить достаточную механическую прочность, приходится увеличивать толщину стенок, а это снижает столь желанный выигрыш в весе.
Кованые диски
Ковка обеспечивает исключительно высокую прочность и жесткость конструкции. Кованый диск держит сильнейшие удары; в крайнем случае он не лопается, как литой, а гнется без образования трещин, что, безусловно, безопаснее. Кроме того, он очень легкий. Сравните: стальной штампованный диск, допустим, для 7-й модели ВМW весит 9 кг, литой алюминиевый - 7,8 кг, а кованый алюминиевый - 6,8 кг. Помять его теоретически можно, но скорее разлетится подвеска, чем помнется закраина кованого колеса. Коррозионная стойкость кованого диска значительно выше, чем литого, а значит, ниже требования к защите поверхности. Если бы не высокая стоимость, обусловленная сложностью технологии, кованые диски, наверное, давно бы вытеснили все остальные - по большинству характеристик кованым нет равных.
Льют и куют диски из алюминиевых и магниевых сплавов. Если расположить легкосплавные диски в порядке «от минуса к плюсу» по чисто техническим параметрам, то ряд будет таким: литой магниевый (легкий, но капризный, быстро растрескивается), литой алюминиевый (нормальный по совокупности качеств), кованый алюминиевый (прочный и легкий) и кованый магниевый (сверхпрочный и легкий). Но при выборе дисков, понятно, не только технические параметры играют роль. Советуем сразу отбросить крайности: магниевые диски, как литые, так и кованые, — большая редкость, их, как правило, делают только на заказ для спортивных машин.
Как выбрать автомобильные диски
Если вы определились с типом диска (литой или кованный и т. д.), то теперь нелишне будет определиться со следующими моментами.
1. Ширина обода.
Запомните! Есть золотое правило: она должна быть на 25-30% меньше ширины профиля шины. Допустим, Вы ищете под шину 195/70 R15. Ширина ее профиля 195 мм. В дюймах это будет 7,68 (надо 195 разделить на 25,4). Отнимите от этой величины 25% или 30% и полученное число округлите до ближайшего значения из стандартного ряда. Получите 5,5 дюйма - обод именно такой ширины нужен для шины 195/70R15.
Предупреждение!
Использование как слишком широких, так и слишком узких дисков (относительно ширины профиля шины) нежелательно: нарушается проектный профиль шины (боковины либо сжаты закраинами обода, либо растянуты на нем), из-за чего ухудшаются ее ездовые характеристики - реакция на поворот, сопротивление уводу, боковая жесткость. Допустимое отклонение ширины обода от нормы составляет 0,5 - 1,0 дюйма для дисков с монтажным диаметром до 14 дюймов; и 1,0 - 1,5 дюйма - для дисков с диаметром 15 дюймов и более. Но лучше, конечно, брать диск точно под шину.
2. Диаметр диска
Полный ряд монтажных диаметров легковых и внедорожных дисков:10, 12, 13, 14, 15, 16, 17, 18 и 19 дюймов. Подавляющее большинство современных автомобилей бегает на 13-, 14-, 15- и 16-дюймовых дисках. В последнее время наблюдается стойкая тенденция к увеличению монтажного диаметра; машины для которых штатными являются, например, 13-дюймовые диски, переводят на 14 дюймовые, 15 на 16 и т.д. Это объясняется стремлением использовать шины низких и сверхнизких серий, поскольку их ездовые качества лучше, чем шин высокого профиля. А чем ниже серия шины, тем меньше в колесе резины и, соответственно, больше металла - ведь наружный диаметр колеса остался неизменным. При использовании стальных дисков монтажный диаметр особо не увеличишь - это приведет к возрастанию массы колеса, что нежелательно. А применение легкосплавных дисков позволяет увеличивать монтажный диаметр диска, не утяжеляя колесо в целом.
Предупреждение! На спортивных версиях автомобилей тормозные механизмы больше, чем на неспортивных, - следовательно, и диски должны быть больше его монтажного диаметра, иначе тормоз упрется в обод. Например, 15-или 16-дюймовый хотя на тюнинговых, спортивных и внедорожных автомобилях могут использоватся и более широкие диски - до 13,5 дюйма
3. Диаметр расположения отверстий крепления (обозначается PCD - Pitch Circle Diameter) и количество этих отверстий. Например, PCD100/4 - 4 отверстия на диаметре 100 мм.
Предупреждение! Поскольку отверстия крепления делают с солидным допуском в плюс по диаметру, можно ошибиться в выборе PCD, если он отличается от штатного на пару миллиметров.
Например, на ступицу с PCD100/4 часто надевают колесо PCD98/4 (98 мм от 100 на глаз не отличишь). Это недопустимо. В этом случае из всех гаек (или болтов) только одна будет затянута полностью; остальные же отверстия 'уведет' и крепеж останется недотянутым или затянутым с перекосом - посадка колеса на ступицу будет неполной. На ходу такое колесо будет 'бить', кроме того, не полностью затянутые гайки будут откручиваться сами собой.
4. Диаметр центрального отверстия диска (устойчивого международного обозначения нет).
У штатных колес автомобиля центральное отверстие, как правило, точно подогнано к ступице оси; на заводах принято центрировать колесо именно по нему - его диаметр является посадочным. Но если Вы покупаете диск в магазине, не удивляйтесь тому, что центральное отверстие может оказаться больше положенного. Производители запчастей часто делают отверстие заведомо увеличенного диаметра и снабжают диск набором переходных колец, что позволяет использовать его на разных моделях автомобилей. Колесо в этом случае центрируют по PCD.
5. Вылет колеса.
Это расстояние между продольной плоскостью симметрии обода и крепежной плоскостью колеса. Вылет может быть нулевым, положительным (ступица диска выпячена наружу относительно середины обода) и отрицательным (ступица утоплена). Для каждой модели автомобиля вылет рассчитывается так, чтобы обеспечивались оптимальная устойчивость и управляемость машины, а также наименьшая нагрузка на подшипники ступиц. Немцы обозначают вылет ET (допустим, ET30 (мм), если его величина положительная, или ET-30, если отрицательная), французы - DEPORT, производители из других стран обычно пользуются английским OFFSET.
Предупреждение! Не ставьте на автомобиль колеса с нештатным вылетом. Уменьшение вылета делает колею колес шире; хотя это немного и повышает устойчивость автомобиля и придает ему стильный гоночный вид, но вместе с тем резко перегружает подшипники ступиц и подвеску. Увеличить же вылет, т.е. сузить колею , как правило, невозможно - диск упрется в тормоз.
Типоразмеры болтов и гаек крепления колеса. Если Вы меняете стальной штампованный диск на легкосплавный, возможно, придется использовать болты (или шпильки) большей длины, чем штатные, - легкосплавный диск толще стального. Кроме того, старый крепеж не подойдет, если на новом диске предусмотрены отверстия, допустим под затяжку на сферу, а имеющиеся у Вас болты (штатные) затягиваются на конус.
Большинство производителей автомобилей комплектуют базовые модели стальными дисками ввиду их низкой стоимости и технологичности изготовления. Штатные стальные колеса изготавливаются с неразборным глубоким бодом и коническими полками для камерных и бескамерных шин постоянного давления.Однако в последнее Время все большее распространение получают колеса из легких сплавов. В чем их преимущества? Легкосплавные диски легче стальных, благодаря чему значительно снижены неподрессоренная и инерционная массы, а это благоприятно сказывается на работе подвески и автомобиля в целом. Улучшается разгонная динамика и активная безопасность автомобиля, снижается вероятность ударов до пробоя, а также расход топлива. Прочные и жесткие, эти колеса позволяют противостоять ударам, идущим от неровностей дороги. Технология производства обеспечивает высокую точность размеров, что сводит к минимуму дисбаланс. Привлекает, конечно, и нарядный внешний вид изделий, их стойкость против коррозии. Маркировка легко-сплавных дисков такая же, как и стальных. Например, 5.5J14H, где 5,5 - ширина обода, 14 - его монтажный диаметр (все размеры в дюймах). Буквы определяют комплекс размеров бортовых закраин. Современные обода проектируют таким образом, чтобы их ширина была на 25-30% меньше ширины профиля шины. Например, для шины 185/70R14 (ширина профиля - 185 мм, или 7,3 дюйма) необходим диск шириной 5,5 дюйма. Конструктивная особенность легкосплавных дисков связана с тем, что все они рассчитаны на бескамерные шины. Поэтому на посадочных полках сделаны кольцевые выступы - хэмпы, которые дополнительно фиксируют борта шины. Очень важным параметром при выборе диска является вылет - расстояние между продольной плоскостью симметрии обода и крепежной плоскостью колеса (см. рис.http://vkontakte.ru/photos.php?act=show&id=-822119_1147... ).
Его величина у каждой модели своя, например, "Волга" - 0; "Жигули" -29; "Самара", "Опель-Корса", "Тойота-Королла" и "Мицубиси-Кольт" 38-40 мм. Ставить на машину диски с несоответствующим ей вылетом не рекомендуется. Допускается уменьшение вылета на 5-7 мм.
Маркировка дисков (см. рис. http://vkontakte.ru/photos.php?act=show&s=1&...)
Автомобильная шина — не просто «резина» одетая на диск колеса, а сложная, многофункциональная конструкция. Основное назначение шины — смягчить толчки и удары, передаваемые на подвеску автомобиля, обеспечить надежное сцепление колеса с дорожным покрытием, управляемость, передать на дорогу тяговые и тормозные силы. В значительной степени от шины зависит коэффициент сцепления, проходимость в различных дорожных условиях, расход топлива и шум, создаваемый автомобилем во время движения. Кроме того, шина должна обеспечить заданную грузоподъемность, надежность и долговечность.
Шины подразделяются:
- в зависимости от конструкции каркаса- на диагональные и радиальные;
- по способу герметизации внутреннего объема- на камерные и бескамерные; - по типу рисунка беговой дорожки- дорожные (летние, всесезонные), универсальные, зимние, повышенной проходимости;
- по профилю поперечного сечения. (СМ. РИС. )
Основные части и детали шины: 1. протектор (беговая дорожка) 2. плечевая зона 3. боковина 4. брекер 5. каркас 6. борт
ДИАГОНАЛЬНЫЕ ШИНЫ. Вам, скорее всего, не придется выбирать шины по этому признаку, так как диагональные уже почти полностью вытеснены с рынка радиальными. Конструкция диагональных шин устарела, но их продолжают выпускать в небольших количествах потому, что они относительно дешевы в производстве. Единственное преимущество этих шин заключается в том, что у них прочнее боковина. Диагональная шина имеет каркас из одной или нескольких пар кордных слоев, расположенных так, что нити соседних слоев перекрещиваются.
КОРД - обрезиненный слой ткани, состоящий из частых прочных нитей основы и редких тонких нитей утка, которые обеспечивают хорошее обрезинивание нитей корда, высокую гибкость и прочность. Корд изготавливается из хлопкового, вискозного или капронового волокна. В настоящее время большее применение находит металлокорд, имеющий нити, свитые из стальной проволоки, толщиной около 0,15 мм. Есть и более дорогие материалы, напр. кевлар, которые не могут получить массового распространения по причине своей дороговизны.
РАДИАЛЬНЫЕ ШИНЫ. В радиальной шине корд каркаса натянут от одного борта к другому без перехлеста нитей. Направление натяжения нитей явствует из названия. Тонкая мягкая оболочка каркаса по наружной поверхности обтянута мощным гибким брекером - поясом из высокопрочного нерастяжимого корда, как правило, стального. Поэтому к надписи radial (радиальная) на боковинах шин часто добавляют belted (опоясанная) или steel belted (опоясанная сталью). Такое расположение слоев корда снижает напряжение в нитях, что позволяет уменьшить число слоев, придает каркасу эластичность, снижает теплообразование и сопротивление качению.
КАРКАС - важнейшая силовая часть шины, обеспечивающая ее прочность, воспринимающая внутреннее давление воздуха и передающая нагрузки от внешних сил, действующих со стороны дороги, на колесо. Каркас состоит из одного или нескольких, наложенных друг на друга слоев обрезиненного корда. В зависимости от конструкции каркаса, размеров, допустимой нагрузки и давления воздуха в шине число слоев корда в каркасе может изменяться от1 (в легковой) до 16 и более (в грузовых, сельхоз.шинах и пр)
БРЕКЕР - часть шины, состоящая из слоев корда и расположенная между каркасом и протектором шины. Он служит для улучшения связей каркаса с протектором, предотвращает его отслоение под действием внешних и центробежных сил, амортизирует ударные нагрузки и повышает сопротивление каркаса механическим повреждениям. В брекере нити корда в смежных слоях пересекаются друг с другом и с нитями корда соприкасающегося слоя каркаса, т.е. расположены диагонально, независимо от конструкции шины. Брекер в радиальных шинах более жесткий, усиленный и малорастяжимый по сравнению с брекером диагональных шин, т.к. он в основном определяет прочностные показатели шин.
ПРОТЕКТОР - массивный слой высокопрочной резины, соприкасающийся с дорогой при качении колеса. По наружной поверхности он имеет рельефный рисунок в виде выступов и канавок между ними, так называемую "беговую дорожку". Протектор предохраняет каркас от механических повреждений, от него зависит износостойкость шины и сцепление колеса с дорогой, а также уровень шума и вибраций. Рисунок рельефной части определяет приспособленность шины для работы в различных дорожных условиях. По типу рисунка протектора шины делятся на четыре основные группы: дорожные (летние, всесезонные), универсальные, зимние, повышенной проходимости.
ПЛЕЧЕВАЯ ЗОНА - часть протектора, расположенная между беговой дорожкой и боковиной шины. Она увеличивает боковую жесткость шины, воспринимает часть боковых нагрузок, передаваемых беговой дорожкой и улучшает соединение протектора с каркасом.
БОКОВИНЫ - часть шины, расположенная между плечевой зоной и бортом, представляющая собой относительно тонкий слой эластичной резины, являющийся продолжением протектора на боковых стенках каркаса и предохраняющий его от влаги и механических повреждений. На боковинах нанесены обозначения и маркировки шин.
БОРТ - жесткая часть шины, служащая для ее крепления и герметизации (в случае бескамерной) на ободе колеса. Основой борта является нерастяжимое кольцо, сплетенное из стальной обрезиненной проволоки. Состоит из слоя корда каркаса, завернутого вокруг проволочного кольца, и круглого или профилированного резинового наполнительного шнура. Стальное кольцо придает борту необходимую жесткость и прочность, а наполнительный шнур - монолитность и эластичный переход от жесткого кольца к резине боковины. С наружной стороны борта расположена бортовая лента из прорезиненной ткани, или корда, предохраняющая борт от истирания об обод и повреждения при монтаже и демонтаже. (СМ. РИС. )
КАК ВЫБИРАТЬ АВТОМОБИЛЬНУЮ ШИНУ?
Ухватить пальцами отросточек облоя, резко его потянуть и отпустить. Если материал качественный, то такой отросточек должен вытягиваться минимум на 2-2,5 своей первоначальной длины и возвращаться к исходному размеру не дольше, чем за одну секунду.
Провести пальцами по внутренней герметичной поверхности шины и потереть их друг об друга. Если талька не ощущается, то такие колеса лучше не покупать.
Проверить дату выпуска.
На боковине автомобильного колеса должен быть штамп ОТК светлой краской (для отечественной резины). Если же на ней есть еще и такие же светлые точки - промежуточный контроль, то это еще лучше.
Через увеличительное стекло просмотреть то место покрышки, которым она сажается на обод, на предмет микроскопических остатков краски. Если обнаружатся остатки краски красного цвета, то на Западе она была уценена из класса «А» до класса «В» из-за косметических дефектов. В общем-то ее покупать можно, она даже сохраняет гарантию. Если - желтой, то это уже класс «С»: нарушение состава каучуковой смеси, гарантии не подлежит, покупать не следует. Если - зеленая краска, то класс «D» - внутренние дефекты. Не покупать ни в коем случае.
ОСОБЕННОСТИ БЕСКАМЕРНОЙ РЕЗИНЫ.
Бескамерную резину можно устанавливать только на диски, имеющие «хампы» - специальные выступы на ободе.
Бескамерная резина гораздо более безопаснее на скорости, т.к. она спускает постепенно.
Бескамерная автомобильная шина до того, как начнет спускать держит, как правило, не один, а несколько проколов.
Не стоит без особой необходимости, вставлять в бескамерную шину камеру. Если в камерной шине воздух, попадающий между камерой и шиной, выходит в атмосферу через сосок или негерметичный обод, то в бескамерной шине он остается плоскими пузырями, которые здорово затрудняют теплоотдачу колеса, и оно часто перегревается в жару при больших скоростях, это чревато.
ОБОЗНАЧЕНИЕ И МАРКИРОВКА АВТОШИН
Обозначение и маркировка шин, выпускаемых в Европе, соответствует Евростандарту, а в США - требованиями Транспортного управления этой страны. Следует отметить, что обозначения и маркировка отечественных и импортных шин по отдельным позициям совпадают, хотя среди них имеются характерные различия. Прежде всего рассмотрим маркировки шин, действующих в Европе:
1 - Пример: 185/65 R15 87Т - размер шины и ее техническая характеристика:
185 - ширина профиля шины в мм.;
65 - отношение высоты профиля к ее ширине, выраженное в процентах;
R - радиальная конструкция шины;
15 - посадочный диаметр обода в дюймах;
87 - индекс грузоподъемности.
Ряд зарубежных фирм указывают максимальную нагрузку (MAX LOAD) в кг и английских фунтах; Т - индекс максимальной скорости, на которую рассчитана шина .
- надпись "Radial" - указывает на радиальную конструкцию шины;
- "Tubeless" - маркировка бескамерной шины. Камерная шина обозначается "TUBE TYPE";
- "M+S" (Mud+Snow -грязь+снег) - тип рисунка протектора. Маркировка обозначает, что шина предназначена для эксплуатации в зимний период года и по грязи.
- цифры 376 - дата выпуска шины: изготовлена на 37-й недели 1996 года
- знак Е одним цифровым индексом (на других шинах может быть двухцифровой индекс) указывает, что шина проверена на соответствие европейскому стандарту безопасности. Индекс в кружке - условный номер страны, где назначенная правительством комиссия провела проверку. Например, Е - проверено в Швеции. Пятизначный (может быть и шестизначный) индекс, нанесенный рядом с кружком, означает номер сертификата, свидетельствующий о положительных результатах проверки, и выданного страной, осуществлявшей проверку;
- страна, в которой находится предприятие-изготовитель шин (Made in Germany -сделано в Германии, Made in Europe - сделано в Европе и т.д.);
ДОПОЛНИТЕЛЬНЫЕ МАРКИРОВКИ, ДЕЙСТВУЮЩИЕ В США:
- DOT - знак, который означает, что шина отвечает нормативным требованиям Транспортного управления США;
- DM AB CD EFG - код, означающий место изготовления, размер и тип шины;
- максимально допустимые в США нагрузка и внутреннее давление воздуха в шине: max Load 545kg (1202 lbs) - 545кг (1202 фунта), max Pressure 300 кПа (44psi) - 3,0 кгс/см2 (44 фунта на квадратный дюйм);
- Plies Tread area:1 Rayon + 2 Steel + 1 Nylon Sidewall: 1 Rayon - особенности конструкции шины: в брекере один слой вискозного корда; два слоя стального и один слой нейлонового корда; в боковине один слой вискозного корда;
- TWI (Tread Wear Indiration) -указатели индикаторов износа (минимально допустимая глубина) рисунка протектора шины. Указатели располагаются равномерно в шести- восьми местах по окружности. Маркировка TWI может быть со стрелкой. Индикатор износа иногда изображается одной стрелкой. Индикатор выполняется в виде выступа высотой 1.6 мм (для легких автомобилей) и располагается в углублении протектора;
- Treadwear 180 - относительная износоустойчивость рисунка протектора. Отвечает специальным стандартным тестам США;
- Traction A - оценка влажностных условий А, В или С ( специальный тест США);
- Temperatyre B - температурная устойчивость на больших скоростях движения А, В или С (специальный тест США);
- Safetywarning - требование техники безопасности при монтаже шины на обод и при использовании шины.
На некоторых моделях шин нового поколения для легковых автомобилей введена дополнительная маркировка. На боковине зимних шин WSP, W160P, W180P, W190P и W210P фирмы "Pirelli" ставится стрелка, указывающая направление вращения колеса. На боковых шинах других фирм наносятся две стрелки с надписью "Rotation" (направление вращения). При сборке колеса необходимо учитывать рекомендации маркировки: направление вращения колеса при движении автомобиля вперед должно совпадать с направлением, указанным стрелкой (стрелками).
ЦВЕТОВЫЕ МЕТКИ НА РЕЗИНЕ:
нет - хорошее качество
красный - косметические дефекты
желтый -нарушение состава каучуковой смеси (без гарантии)
зеленый - внутренние дефекты
Индекс грузоподъемности, кг/колесо
60 - 250
62 - 265
64 - 280
66 - 300
68 - 315
70 - 335
72 - 355
74 - 375
76 - 400
78 - 425
80 - 450
82 - 475
84 - 500
86 - 530
88 - 560
90 - 600
Индекс максимальной скорости, км/ч
I - 100
K - 110
L - 120
M - 130
N - 140
P - 150
Q - 160
R - 170
S - 180
T - 190
H - 210
V - 240
VR - 210-240
ZR - от 240
Радикальное средство против скольжения
Металлические шипы на автомобильных покрышках появились уже в начале ХХ века. Тогда их устанавливали не только для лучшего сцепления с дорогой, но и для увеличения износостойкости шин, которые в те времена были из кожи или из цельнолитой резины. Позже, после изобретения пневматических шин, интерес к шипам ослабел. Их массовому применению мешали несовершенство конструкции и низкая износостойкость стальных штифтов. Однако в 30-е годы шины спортивных автомобилей часто оснащались шипами. Как правило, для их установки в покрышках делали сквозные отверстия — изнутри вставляли стальной болт-грибок, а снаружи его фиксировали обычной гайкой. Представляете, сколько весили такие шины! Лишь в конце 50-х годов в Скандинавии появились шипы традиционной для сегодняшних дней конструкции. За основу была взята обычная стальная заклепка, в тело которой запрессовывалась твердосплавная вставка. В таком виде шип монтировался в протектор шины. Неоспоримые преимущества шипованых шин в зимних условиях быстро оценили водители не только скандинавских, но и других европейских стран. В погоне за безопасностью в шипованые шины переобувались не только легковые автомобили, но и грузовики, автобусы, тяжелая строительная техника. И тут тревогу забили дорожники-с появлением шипованых шин у них прибавилось работы! По окончании зимнего сезона на асфальте оставались колеи- шипованое колесо работало как фреза. Особенно пагубным оказалось воздействие шипованых шин на немецкие автобаны, большую часть зимы очищенные от снега и льда. Неудивительно, что первыми восстали против шипов именно немцы-с 1975 года использование шипованых шин на территории Германии запрещено. Их примеру вскоре последовали многие европейские страны- там либо полностью запретили использовать шипованые шины, либо ввели ряд ограничений. Кроме того, как показали исследования ученых, шипованые зимние шины представляют серьезный риск для здоровья людей. Частицы дорожного покрытия, которые вырываются шипами, превращаются во вредную для дыхания пыль, от которой страдают прежде всего астматики. По мнению исследователей, подобные загрязнения становятся причиной преждевременной смерти 1800 человек ежегодно. Ученые считают, что частицы асфальтовой пыли более опасны, чем выхлопные газы. Сейчас в Европе не так много стран, где можно использовать шипы противоскольжения. Соответственно, немного и фирм, занимающихся их производством. Как правило, шипованые шины покупают в том случае, когда предстоят частые поездки по заснеженым и обледенелым дорогам. В этом случае шипованые шины будут незаменимы. На голом асфальте шины с шипами уступают по управляемости и торможению обычным зимним шинам. (рис)
Конструкция
Как и 50 лет назад, шипы противоскольжения сегодня состоят из двух деталей: корпуса и твердосплавной вставки. Задача корпуса- удержать шип в теле протектора в течение всего срока службы шины. А штифт должен вгрызаться в дорожную поверхность, увеличивая коэффициент сцепления на скользком покрытии. Для изготовления вставок используется карбид вольфрама (WC) с примесью карбидов титана и ниобия (TiC, NbC) и еще ряда соединений. Каких- не сообщается: у каждого производителя, конечно, есть свой, фирменный, рецепт твердого сплава. Но известно, что такие редкоземельные добавки позволяют достичь твердости 1500 единиц по Виккерсу (для сравнения- шестерни в коробке переключения передач автомобиля имеют в три раза меньшую поверхностную твердость!). Понятно, что для работы на льду или снегу такая прочность не нужна, но зато на асфальте твердосплавная вставка изнашивается с той же интенсивностью, что и протектор шины. Естественно, с учетом разницы площадей контакта. Основной объект усовершенствования- корпус шипа, а точнее, его форма и материал. Поначалу корпуса шипов были стальными. Но как только развернулась борьба за сохранение дорожного покрытия и масса шипов была ограничена, появились модели с пластмассовыми корпусами. Масса пластикового шипа в сборе со вставкой составляет всего 0,7 грамма, меж тем как самые легкие стальные шипы весят 1,1 грамма. К сожалению, пластмасса иногда не выдерживает нагрузок в сочетании с низкой температурой, и шипы вываливаются из тела протектора.
В последнее время практически у всех фирм-производителей шипов появились модели с алюминиевыми корпусами. Легированный алюминий по прочности приближается к стали, а по весу- к пластмассе. Например, шип Kometa Marathon финской фирмы Tikka-Nastat OY весит 0,9 грамма. И к тому же покрыт тефлоном- чтобы облегчить монтаж в посадочное отверстие и увеличить коррозионную стойкость. Кстати, коррозия- это тот бич, который заставляет усложнять форму корпуса. У основания традиционного шипа имеется всего один фланец, и в зазор между корпусом и резиной постепенно проникают соль, песок и вода- начинается пагубный процесс коррозии. Чтобы поставить преграду на пути агрессивной среды, на корпусе шипов делают по два, а то и по три фланца. К тому же многофланцевые шипы прочнее держатся на своих местах. Но у них есть свой недостаток- они сложнее в изготовлении и, соответственно, дороже. Шипы делятся также по способу производства – штампованные и точеные. Последние стоят на порядок дороже, так как в этом случае каждый шип обрабатывается отдельно. Как отличить друг от друга пластиковый и стальной шип, однофланцевый и трехфланцевый, если известны лишь их "имена"? Пока единой системы маркировки для этих изделий нет, а потому каждая фирма вольна окрестить свои шипы по-своему. Как правило, в цифровом обозначении модели зашифрованы диаметр основания, общая высота шипа (включая твердосплавную вставку) и количество фланцев. Например, шип U8-11-2 французской фирмы Ugigrip имеет основание диаметром 8 мм, высоту 11 мм и двухфланцевый корпус. Как показывает практика, хороший шип не может улучшить характеристики заурядной зимней шины, и наоборот. Это раньше достаточно было прийти в мелкую мастерскую, где в шине без всякого специального оборудования насверлят отверстий и насажают туда любых шипов.
А сейчас все лидеры в производстве зимних шин если и доверяют ошиповку сторонним фирмам, то строго держат процесс под своим контролем. И разрабатываются современные зимние покрышки под конкретный тип шипов. Протектор состоит из двух слоев резины: поверхностный, более мягкий, отвечает за сцепные свойства с дорогой, а внутренний твердый слой плотно удерживает шипы, вставленные в отверстия специального профиля- в виде перевернутой буквы Т. Кроме того, под каждым шипом предусмотрена специальная подушечка из мягкой резины- чтобы при движении по твердой поверхности шип утапливался внутрь шины, меньше царапая дорогу и увеличивая комфорт при езде. Импортные шины в основном поставляются к нам в неошипованом варианте, но с уже специальными гнездами под шипы. Отечественные шины, как правило, идут без гнезд, но со специальной разметкой, ориентируясь по которой в специализированных фирмах с помощью специального оборудования делают гнезда под шипы. После покупки шипованые шины должны пройти «обкатку». Она подразумевает плавное трогание и торможение, а также небольшую скорость (60-80 км/час) на первых пятистах километрах эксплуатации шипованых шин. Также стоит чаще проверять давление в шинах. Это позволит избежать преждевременного износа шипов и их выпадания из шины. (рис)