Попробуем разобраться, какую роль играет сталь в качестве ножа?
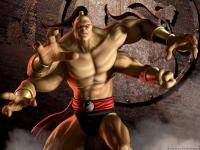
Самый распространенный вопрос, который задает человек, выбирающий нож – а из какой он стали? И ответ на этот вопрос часто определяет решение этого самого человека относительно приобретения этого самого ножа. И этим пользуются производители. В том числе и мы.
Попробуем разобраться, какую роль играет сталь в качестве ножа, какие вообще бывают железки и как с этим жить.
Как говорил незабвенный И.А. Скрылев – нож, это заточенная пластина металла. В обшем то он прав. И основное предназначение ножа – резать (иногда колоть, иногда – ковырять, открывать консервные банки и цинки, отжимать двери, отрубать горлышки бутылкам…) И реализуется это клиновидной формой рабочей части обсуждаемого предмета. Она так и называется – клинок. Далее мы и будем рассматривать только клинки и клинковые материалы.
Как работает клинок – да элементарно. Прикладывая к полосе клинка определенные усилия, мы создаем на режущей кромке (далее РК) достаточно высокие давления, которые превышают прочность разрезаемого материала. На самом деле механизм реза более сложен, важную роль играет еще и микрогеометрия РК и характер ее взаимодействия с разрезаемым материалом, но, в общем и целом, надо понять, что создание достаточного давления на РК (это может требовать и совсем небольших усилий) – необходимое для реза условие. Как правило, у реза есть 2 компонента – собственно давление и протяг РК по разрезаемому материалу. В зависимости от задачи может превалировать один или другой компонент, но можно выделить “рез давление” и “рез потягом”. С первым мы имеем дело, например шинкуя салат или строгая твердую деревяшку, со вторым – разрезая кожу или перерезая пеньковый канат. Собственно, каждый по своему опыту примерно представляет, как нужно резать каждый конкретный материал.
Вот так незаметно для себя мы сделали важнейший вывод – задачи бывают разными, способы их решения – тоже разные, и самое главное – они требуют разного инструмента. В переводе на русский – для каждой задачи будет оптимален свой нож. Нарезать хамон – один, рубить гвозди – другой…. Даже для более узкого спектра задач, если важно удобство и производительность, удобнее пользоваться разными ножами. Например, скатка профессионального повара-“европейца” содержала до 27 предметов, из которых более 20 ножей. А если добавить суда еще и японию… Тем не менее, большинство людей вполне обходятся на кухне парой-тройкой ножей (а то и одним, который еще Ленина видел) и это их вполне устраивает… Собственно, баланс между удобством выполнения отдельных задач и количеством (а соответственно, и ценой) инструмента – личное дело каждого.
Чем же отличается хороший нож от плохого? На мой взгляд, тем, что позволяет выполнить конкретную задачу максимально качественно, быстро и комфортно. Не важно, что мы делаем, чистим яблоко, режем вражину или рубим рельс – нас либо устраивает, как с этим справляется нож, либо нет. Еще один важный момент – нож, отлично справляющийся с одним, может быть совершенно непригоден для другого.
Если сконцентрироваться на клинках, то мы можем вспомнить, что чистить яблоко или картошку даже очень качественным “ломиком” ой как неудобно… А попытка открыть банку тушенки янакибой скорее всего приведет к поломке ножа.
А вот тут мы сделали еще один важный вывод: каждой задаче – свою геометрию клинка.
Геометрию клинка можно разделить на общую, геометрию спусков и геометрию и микрогеометрию РК. Забегая чуть дальше, скажу, что именно выбор правильной геометрии под задачу (ну или спектр задач) есть основа хорошего ножа (да здравствует Прокопенков !!!). А материал клинка – средство реализации этой самой геометрии.
Вот, наконец-то, дошли до клинковых материалов. Отправив всякую экзотику в сад, рассмотрим стали, из которых могут изготавливаться клинки ножей.
Что же такое сталь? А это сплав, в котором железа не менее 45% и больше, чем любого другого компонента. Стоп, а как же про “сплав железа с углеродом, в котором углерода меньше 2.14%”? Отвечу – это было давно и неправда. И с тех пор много воды утекло.
Какими же свойствами должна обладать сталь для клинка?
Твердость!!! …. И будете правы. Здесь вроде бы все понятно. Сталь должна быть как минимум тверже, чем разрезаемый материал. От твердости зависит износостойкость (для разных сталей по разному), а значит и способность сохранять заточку, сопротивление смятию (от этого например, зависит способность сохранять тонкую РК ) и целый ряд других свойств. Исторически сложилось, что твердость закаленных сталей наиболее часто определяют и по методу Роквелла, шкала С (обозначается HRc). Обычно твердость термообработанных клинковых сталей лежит в диапазоне 42-67 HRc, наиболее часто – 52-61. При более детальном рассмотрении надо понимать, что как правило, твердость стали – типа средней температуры по больнице, ибо у разных структурных элементов она разная. Более того, к одной и той же общей твердости можно придти сильно разными путями и с сильно разным результатом.
Прочность. А вот здесь все в кучу. Помимо собственно прочности, то есть способности выдерживать без разрушения определенные нагрузки, сюда часто относят и то, что в английском достаточно емко описывается понятием toughness – однозначного перевода на русский язык нет, наукообразно все это называется “критерии (или факторы) конструкционной надежности”. Здесь и работа разрушения и ударная вязкость и параметры пластичности и трещинностойкости и еще около 60 параметров. Короче, все это вместе определяет, насколько чувствительна сталь к различным экстремальным нагрузкам и насколько “надежен” будет нож из нее. На самом деле, как это все мерить и каким параметрам отдать приоритет – очень сложная задача. Скажу одно – в подавляющем большинстве случаев геометрия заруливает все остальные факторы вместе взятые.
Способность держать заточку. Комплексный параметр, крайне сильно зависящий от структуры стали. В последнее время заменил твердость в качестве маркетингового фетиша.
Острота заточки и агрессивность реза. Здесь все субъективно. Как и предыдущий параметр, сильно зависит от структуры стали и правильной заточки.
Коррозионная стойкость. По этому параметру многие делят ножевые стали на “углеродки” и “нержавейки”. На самом деле все сложнее, и будет ли конкретная сталь стойкой в конкретных условиях, вопрос интересный.
Выше пару раз прозвучало слово “структура”, которая каким то образом влияет на свойства. Что же это такое и с чем ее едят? Как мы уже определились, сталь – это некоторый сплав. И элементы, входящие в этот самый сплав, определенным образом взаимодействуют, формируя под влиянием механической и термообработки (далее ТО) различные фазы, соотношением и свойствами которых (а так же характером их взаимодействия между собой) и определяется структура (и свойства) стали. В подавляющем большинстве случаев структура термообработанной ножевой стали состоит из мартенсита (что это такое, объяснять долго и нудно и все равно не поймете, считайте что это твердая и хрупкая составляющая матрицы) некоторого количества остаточного аустенита (мягкого и пластичного) и фаз-упрочнителей (чаще всего карбидов).
Абстрагируясь от частностей, можно сказать, что структура стали зависит от ее состава (читай марки) и того, что с ней сделали. Причем, вторая часть часто важнее первой.
Теперь собственно о ножевых сталях. Единой классификации нет, наверное проще будет плясать от назначения. Итак, в качестве ножевых используются инструментальные стали (для режущего инструмента и штамповые) и близкие к ним по свойствам изностостойкие стали (подшипниковые, валковые), рессорно-пружинные, конструкционные высокопрочные и т.д. Рассмотрим основные классы. При этом буду придерживаться классификации, принятой для инструментальных сталей (для сталей другого целевого назначения буду делать комментарии)
Стали типа наших У7-У16 и буржуйской 1095. Сюда же можно отнести легированные марганцем стали (в том числе и любимую многими 65Г). Весьма популярны, но, на мой взгляд, недостатков намного больше, чем плюсов. В первую очередь, хотя это многих удивит, низкая прочность и ударная вязкость (без ковки и/или термоциклической обработки). Во вторых, как это опять же не удивительно, сложность ТО – в первую очередь узкий интервал закалочных температур (особенно, для эвтектоидных сталей) – стоит чуть перегреть – пиши пропало. В третьих – низкая износостойкость, несмотря на высокие достижимые значения получаемой твердости. Низкая закаливаемость и прокаливаемость, высокая деформация при закалке. Низкая стабильность свойств. Ржавеют опять же.. Все вышесказанное не относится к ножам Мастеров – в их исполнении углеродка может быть очень неплоха. Из плюсов – при должном навыке можно получить очень приличный нож при минимуме оборудования.
А теперь попробую поподробнее.
Инструментальные углеродистые стали в соответствии с ГОСТ 1435–90 маркируют буквой «У» и числом, указывающим среднее содержание углерода в десятых долях процента. Для изготовления инструмента применяют качественные стали марок У7–У13 и высококачественные стали марок У7А–У13А, а так же стали, легированные марганцем и кремнием (например, У7Г, У15С).
По структуре стали подразделяются на доэвтектоидные (У7), эвтектоидные (У8-У9) и заэвтектоидные (У10-У16) По механическим свойствам и назначению углеродистые стали подразделяются на:
» стали повышенной вязкости (У7–У9) для изготовления инструмента с высокой режущей способностью, подвергающегося ударным нагрузкам (зубила, кернеры и т.д.). К этой же группе можно отнести рессорно-пружинные стали типа 60-75Г.
» стали высокой твердости (У10–У13) для изготовления режущего инструмента, не подвергающегося ударным нагрузкам (напильники, шаберы и т. д.). Сталь У16 применяется в основном для изготовления износостойких втулок и склонна к графитизации.
Твердость окончательно термически обработанного инструмента из углеродистых сталей обычно лежит в интервале 57–65 HRc. Стали требуют аккуратного шлифования из-за возможности образования прижогов и мягких пятен. После шлифования желателен низкий отпуск.
Свойства углеродистых сталей могут быть заметно улучшены термоциклической и термомеханической обработкой. В некоторых случаях будет уместной зонная закалка или отпуск.
В данном пункте будут рассмотрены только низко- и среднелегированные стали. Эти стали подразделяются на стали неглубокой и глубокой прокаливаемости. По назначению – инструментальные и подшипниковые ШХ15 – к стали Х.
Из наиболее популярных хочется отметить
» Х (ШХ15)
» 9ХФ (90ХФМ)
» 11ХФ (11Х)
» 13Х
» ХВГ (ХСВГ, ХСВГФ)
» В2Ф и ХВ4Ф (ХВ5)
Данная группа сталей в общем и целом имеет лучшую комбинацию свойств, не зря например, ШХ15 одна из самых популярных у российских мастеров железок.
Как правило, стали, легированные хромом, вольфрамом, молибденом и ванадием. Исторически наиболее популярна Р6М5 (М2). При правильной ТО сталь с неплохим комплексом свойств. Но, все же, уступает высокованадиевым сталям предыдущей группы. В последнее время на эксклюзивных моделях появляются и другие выстрорезы, как правило высокованадиевые порошковые. Интегральное мнение – стали весьма неплохи, но тот же (и даже более высокий) уровень свойств можно получить на сталях попроще и с более простой ТО.
Отдельную группу составляют стали с интерметаллидным или карбидным и интерметаллидным упрочнением – о них дальше.
Как правило это стали обрабатываемые на вторичную твердость (подобно быстрорезам). Основное применение – инструмент для холодной деформации, теплостойкие подшипники, детали топливной аппаратуры. В последнее время популярны на дорогих авторских ножах.
В силу доступности и раскрученности чаще всего используются порошковые буржуинские стали. Из наиболее популярных – CPM 3V, CPM 10V, Vanadis 4-10 и т.д.
На мой взгляд, стали обеспечивают хорошее сочетание стойкости РК и механических свойств. При минимальном уходе стали достаточно коррозионнно-стойки в неагрессивных средах.
Чаще всего хромистые, хромо-молибденовые стали, иногда легированные другими элементами. В последнее время самые распространенные стали для ножей.
Надо понимать, что все мартенситные коррозионно-стойкие стали предрасположены к питтинговой коррозии, особенно в средах, содержащих хлориды.
95Х18
Х18МФ
Х13М (Х14М)
65Х13
50Х14МФ,
90Х18МФ
ЭП766 (95Х13М3К3Б2Ф).
Отдельно стоит выделит вторично-твердеющие стали типа 154 CM, ATS-34, BG 42, ЭП766 (95Х13М3К3Б2Ф) (правда, большинство производителей обрабатывает их на первичную твердость) и высокованадиевые порошковые стали типа S30V, S60V, S90V, S110V и т.д. Несколько особняком стоят высокохромистые сверхвысокоуглеродистые стали типа ZDP-189, Cowry-X, Supracor (MPL-1)
Стали последних трех групп де-факто стали стандартом для качественных серийных и авторских буржуйских ножей.
По назначению – быстрорежущие, штамповые и с высоким сопротивлением пластической деформации. Для клинков могут применятся и некоторые конструкционные мартенситно-стареющие стали, в первую очередь нержавеющие высокопрочные и сверхпрочные. Из наиболее типичных представителей – ЭП853 (03Х11Н10М2Т2). До сих пор ни в России (у нас только Мелита), ни в мире нет заметного интереса к этой очень интересной группе сталей. При том, что некоторые из них обладают уникальными характеристиками. Недостатки – высокая стоимость, малая доступность, сложная ТО (часто именно ТМО), низкая (очень относительно) стойкость по абразивным материалам.
Перспективные материалы с неклассической структурой. По ряду параметров обладают уникальными характеристиками. Есть много нерешенных вопросов. Насколько мне известно, для клинков ножей в настоящее время не используются, но, на мой взгляд имеют в этом отношении хорошие перспективы.
Какая сталь самая лучшая? А таковой нет, точнее, в каждом отдельном случае будут оптимальны разные стали. На мой взгляд, стоит руководствоваться следующей схемой: задача=>геометрия=>сталь=>ТО. Если нет четких представлений – лучше выбирать геометрию и производителя.
Что думаешь про сталь Х12МФ? Ничего не думаю. Все зависит от того, кто и что с ней сделал. При правильном подходе очень неплохая сталь для универсального ножа. Что не означает, что Вам достанется именно такая. Репутация производителя и мнения реальных пользователей его продукции помогут сделать правильный выбор.
А что скажешь за дамаски и булаты? Тем более ничего не скажу. Вопрос свойств авторского материала – это вопрос Мастеру.
Я хочу, что бы мой нож рубил рельс без повреждения и расщеплял волос – какую сталь посоветуешь? Такой большой, а в сказки веришь.
Я слышал, что есть ракетная сталь (сталь от лопатки турбины, брони танка, большого адронного коллайдера) – она самая лучшая? Я тоже много чего слышал. Гораздо меньше видел.
Скольких кабанов можно разделать нормальным ножем? Кабаны бывают разные, разделывают все по разному. В принципе, ножа из любой пристойной стали при нормальной квалификации раздельщиков хватает на то, что бы разобрать пару кабанчиков среднего размера.
Я метнул нож в промерзшее дерево, а он бзыньк и сломался… Сталь хреновая? ПОЗДРАВЛЯЮ!!!
У меня отец сделал нож – я двадцать лет им пользуюсь и ни разу не подтачивал – есть что нибудь похожее? Ну, либо пользуетесь странно, либо нож тупой как сибирский валенок. Я лично таких ножей делать не умею. Но я слышал о человеке, который без подточки пользуется 40 лет ножем, изготовленным его дедом. Его и спросите.
Говорят, что нержавейка “мылит”? Бывает. Виной всему либо плохая ТО либо неудачная заточка.
Что лучше – плохая ТО на хорошей железке или наоборот? Хорошая ТО на хорошей стали. Сталь и ее термообработка неразделимы как Ленин и Партия. Иногда получается сделать из говна конфетку (причем не факт, что результат будет воспроизводимым), а наоборот – и того проще.
Я вот купил нож от Х из 95Х18 – мне понравился, а через полгода купил нож от Y из этой же стали, а он полное говно. Почему так? Причин может быть много, от использования сталей разного металлургического качества до тонкостей с заточкой. Не бывает стали 95Х18 – бывает сталь 95Х18 от <имярек>
Я купил дорогущий нож из CPM 10V, порезал им морепродукты и оставил на ночь, а с утра он был весь в рыжих пятнах! И это за такое бабло… как дальше жить? Так же как и раньше, без ножа из CPM 10V, оно Вам не надо. Не особо замороченная нержавейка спасет отца русской демократии
95Х18 Одна из самых распространенных российских нержавеек. Недорогая и не особо замороченная. При правильной ТО обеспечивает вполне сносный результат. Собственно, по результатам тестов уважаемого Андрея (Taledo) наша 95 на ноже Беркем заняла первое место, обойдя ближайшего преследователя более чем вдвое и показав примерно такой же результат, как порошки на ножах известных буржуйских контор. Используем для недорогих ножей.
Cronidur 30 – уже стала нашей “фирменной” сталью. Благодаря легированию азотом (типично 0.3С 0.4N 15Cr 1Mo 1Si) сталь имеет высокую прочность и пластичность. Хорошо держит тонкую кромку и обладает агрессивным резом. Обладает очень высокой для сталей мартенситного класса коррозионной стойкостью. Хорошая сталь для универсального/кухонного/боевого ножа.
CPM S30V – одна из лучших по комплексу свойств порошковых нержавеющих сталей. По результатам тестов, наша тридцатка заметно обошла ее же на известных буржуинских ножах. К сожалению, ввиду кончины Крусибла перспективы ее дальнейшему использованию пока непонятны.
CPM S90V – высокованадиевая порошковая нержавейка. Благодаря высокому содержанию карбидов ванадия обладает высокой абразивной износостойкостью. По результатам тестов наша 90 показала примерно такую же способность удерживать заточку, как и буржуинская при более высокой агрессивности реза. В виду ситуации с Крусиблом в ходу скорее всего будут аналоги от других производителей.
CPM S110V Нержавеющая сталь с экстремально высоким содержанием твердых карбидов. Статистики пока не набралось. Доступность ограничена, перспективы туманны.
CPM 3V одна из моих любимых сталей. Сочетает высокую износостойкость и очень хорошие механические свойства. Обладает крайне агрессивным резом и достаточно высокой коррозионной стойкостью (сталь не “нержавейка”). Доступность ограничена.
CPM 10V – на сей момент чемпион по удержанию РК. Приличная механика. Хороший выбор для скиннера или универсального охотничьего ножа высшего класса. Скорее всего, в будущем будет использоваться аналоги от других производителей.
ZDP 189 и Cowry-X – Высокохромистые сверхвысокоуглеродистые стали. Позволяют получить очень высокую твердость (до HRc 69). Обладают агрессивным резом. Требуют аккуратного обращения, несмотря на высокое содержание хрома (20%) не абсолютно коррозионнно-стойкие. Применение – кухня и ножи высокого класса со сложной геометрией клинка.
Duratech CV-20 – порошковая нержавейка, по свойствам примерно между S30V и S90V. Пока на стадии тестирования.
CV-134 Высокованадиевая штамповая сталь порошкового передела. Обеспечивает достаточно высокую износостойкость при приличной механике и коррозионной стойкости. Хороший выбор для охотничьих ножей высокого класса.
1. Вторично твердеющая сталь со сверхтвердыми комплексными карбидами. .
2. Высокоэнтропийный сплав со сверхтвердыми комплексными карбидами. Обещает другой уровень свойств, чем материалы с классической структурой.
Своим ученикам обязательно посоветую прочесть, а если что не поймут, на пальцах им объясню.
Спасибо Михаил Майкл Савельев.