Кратко по баллонам
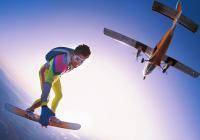
1. Алюминий - тяжело, дешево, неудобно, долгий срок службы, длинный. Основной недостаток - малый объем и малое максимальное заправочное давление 3000 psi - верхний предел.
2. Кевлар=композит - дорого, легко, также неудобно , требует поверки раз в 5 лет, есть короткие баллоны. Алюминиевая или пластиковая колба обмотанная толстым слоем кевларовым волокном с полимерной смолой. Максимальное заправочное давление - 4500 psi, но больше 4000 Psi дают редко. Больший внутренний объем вкупе с большим заправочным давлением позволяют увеличить количество выстрелов с одной заправки примерно на 40%. Основное преимущество - маркеры меняются, баллон остается. Раз в 5 лет требуется проходить переопрессовку. Подробностей не знаю, т.к. не знаю тех кто на это заморачивался.
ИМХО - кевлар оптимум. Т.к. ты все равно к нему придешь, то лучше сделать это без потери времени и средств на алюминий.
Теперь о регуляторах.
1. "Низкодав" - 450 psi. Всего несколько электронных маркеров высокого класса категорически требуют применять низкодавы. Большинство современных электронных маркеров работают и с регуляторам на 450 и на 850 psi. Считается, что на низкодаве электроника меньше расходует воздуха... не берусь судить.
2. "Высокодав" - 850 psi. Все механические маркеры в стоковых вариантах требуют применять высокодав. Кокеры - механика, потому нужен высокодав. Это связано с тем, чито при механическом управлении подачей газа требуется большее давление в системе для движения более массивных подвижных деталей.
Единственное что, я не знаю точно требований "суперсток 05", возможно там стоит система работы на низком давлении... Но в любом случае, высокодав универсальнее в применении ибо работает даже если прикрутить свой баллон к прокатному типпману.
Но кевларовые все еще можно встретить ;)
ИМХО - нинзя на 50 кубиков (4500psi) явно меньше и легче прокатного люминя на 48 кубиков (3000psi) только дороже в разы ;(
p.s. полностью согласен по поводу потери времени и средств на алюминиевый баллон, но каждый видимо должен это пройти сам...
так сказать наступить и на эти грабли ;)
теперь вместо Арамида (Kevlar) применяют Углерод (Carbon Fiber)
а арамид небось наши запатентовали в НИИ стали? :))
лень в инете искать ;))
Вообще углеродное волокно прочнее на растяжение,
только жаль дорогое и вредное его производство.
А кевлар у нас в бронижилетах в основном использовали вроде.
Помню когда у нас первые кевларовые авто динамики появились (буржуйские)...
вроде углерод твердый и ломкий?
достаточно трудно"
http://ru.wikipedia.org/wiki/%D0%9A%D0%B0%D1%80%D0%B..._(%D0%BC%D0%B0%D1%82%D0%B5%D1%80%D0%B8%D0%B0%D0%BB)
И на закусь про Кевлар
http://ru.wikipedia.org/wiki/%D0%9A%D0%B5%D0%B2%D0%B...
Применение
Изначально материал разрабатывался для армирования автомобильных шин, в этом качестве он используется и теперь. Кроме того, кевлар используют как армирующее волокно в композитных материалах, которые получаются прочными и легкими.
Кевлар используется для армирования медных и волоконно-оптических кабелей (нитка по всей длине кабеля, предотвращающая растяжение и разрыв кабеля), в диффузорах акустических динамиков и в протезно-ортопедической промышленности для увеличения износостойкости частей углепластиковых стоп.
Кевларовое волокно также используется в качестве армирующего компонента в смешанных тканях, придающего изделиям из них стойкость по отношению к абразивным и режущим воздействиям, из таких тканей изготовляются, в частности, защитные перчатки и защитные вставки в спортивную одежду (для мотоспорта, сноубординга и т. п.). Также он используется в обувной промышленности для изготовления антипрокольных стелек.
[править] Использование в бронежилетах
Механические свойства материала делают его пригодным для изготовления пуленепробиваемых жилетов. Это одно из самых известных применений кевлара.
В 1970-е годы одним из наиболее значительных достижений в разработке бронежилетов стало применение армирующего волокна из кевлара. Разработка бронежилета из кевлара Национальным институтом правосудия (англ. National Institute of Justice) происходила в течение нескольких лет в четыре этапа. На первом этапе волокно тестировалось, чтобы определить, способно ли оно остановить пулю. Второй этап заключался в определении количества слоев материала, необходимого для предотвращения пробивания пулями различного калибра и летящими с разной скоростью, и разработке прототипа жилета, способного защищать сотрудников от наиболее распространенных угроз: пуль калибра .38 Special и .22 Long Rifle. К 1973 году был разработан жилет из семи слоев волокна из кевлара для полевых испытаний. Было установлено, что при намокании защитные свойства кевлара ухудшались. Способность защищать от пуль также уменьшалась после воздействия ультрафиолета, в том числе солнечного света. Химчистка и отбеливатели также негативно сказывались на защитных свойствах ткани, также как и неоднократные стирки. Чтобы обойти эти проблемы, был разработан водостойкий жилет, имеющий покрытие из ткани для предотвращения воздействия солнечных лучей и других отрицательно влияющих факторов.
[править] Температурные свойства
Кевлар сохраняет прочность и эластичность при низких температурах, вплоть до криогенных (-196 °C), более того, при низких температурах он даже становится чуть прочнее.
При нагреве кевлар не плавится, а разлагается при сравнительно высоких температурах (430—480 °C). Температура разложения зависит от скорости нагрева и продолжительности воздействия температуры. При повышенных температурах (более 150 °C) прочность кевлара уменьшается с течением времени. Например, при температуре 160 °C прочность на разрыв уменьшается на 10-20 % после 500 часов. При 250 °C кевлар теряет 50 % своей прочности за 70 часов.
Материалы отличаются высокой прочностью, жесткостью и малой массой, часто прочнее стали, но гораздо легче (по удельным характеристикам превосходит высокопрочную сталь, например 25ХГСА).
Вследствие дороговизны (при экономии средств и отсутствии необходимости получения максимальных характеристик) этот материал обычно применяют в качестве усиливающих дополнений в основном материале конструкции.
Основные сведения
Основная составляющая часть углепластика — это нити углерода. Такие нити очень тонкие (примерно 0.005-0.010 мм в диаметре[1].), сломать их очень просто, а вот порвать достаточно трудно. Из этих нитей сплетаются ткани. Они могут иметь разный рисунок плетения (елочка, рогожа и др.).
Для придания еще большей прочности ткани из нитей углерода кладут слоями, каждый раз меняя угол направления плетения. Слои скрепляются с помощью эпоксидных смол.
Применяется для изготовления легких, но прочных деталей, например: велосипеды, кокпиты и обтекатели в Формуле 1, спиннинги, мачты для виндсерфинга, бамперы, пороги, двери, крышки капотов на спортивных автомобилях, несущие винты вертолетов.
Нити углерода обычно получают термической обработкой химических или природных органических волокон, при которой в материале волокна остаются главным образом атомы углерода.
Температурная обработка состоит из нескольких этапов.
Первый из них представляет собой окисление исходного (полиакрилонитрильного, вискозного) волокна на воздухе при температуре 250 °C в течение 24 часов. В результате окисления образуются лестничные структуры.
После окисления следует стадия карбонизации — нагрева волокна в среде азота или аргона при температурах от 800 до 1500 °C. В результате карбонизации происходит образование графитоподобных структур.
Процесс термической обработки заканчивается графитизацией при температуре 1600-3000 °C, которая также проходит в инертной среде. В результате графитизации количество углерода в волокне доводится до 99 %.
Помимо обычных органических волокон (чаще всего вискозных и полиакрилонитрильных), для получения нитей углерода могут быть использованы специальные волокна из фенольных смол, лигнина, каменноугольных и нефтяных пеков. Кроме того, детали из карбона превосходят по прочности детали из стекловолокна. Детали из карбона обходятся значительно дороже аналогичных деталей из стекловолокна.
Дороговизна карбона вызвана, прежде всего, более сложной технологией производства и большей стоимостью производных материалов. Например, для проклейки слоев используются более дорогие и качественные смолы, чем при работе со стеклотканью, а для производства деталей требуется более дорогое оборудования (к примеру, такое как автоклав).
Недостатком карбона является боязнь «точечных» ударов. Например, капот из карбона может превратиться в решето после частого попадания мелких камней. В отличие от металлических деталей или деталей из стеклоткани, восстановить первоначальный вид карбоновых деталей невозможно. Поэтому, после даже незначительного повреждения всю деталь придется менять целиком. Кроме того, детали из карбона подвержены выцветанию под воздействием солнечных лучей.
Наконец, когда приходит время для замены детали, существует целый ряд относительно простых шагов, которые могут быть предприняты для утилизации пластмассы, стали и алюминия. Углепластик же не так легок и дешев в переработке и поэтому его вторичное использование под большим вопросом
Производство
Прессование. Углеткань выстилается в форму, предварительно смазанную антиадгезивом (например, мыло, воск, воск в бензине, Циатим-221, кремнийорганические смазки). Пропитывается смолой. Излишки смолы удаляются в вакууме(вакуум-формование) или под давлением. Смола полимеризуется, иногда при нагревании. После полимеризации смолы изделие готово.
Трубы и иные цилиндрические изделия производят намоткой. Форма волокна: нить, лента, ткань. Смола: эпоксидная или полиэфирная. Возможно изготовление форм из углепластика в домашних условиях, при наличии опыта и оборудования.
1 - http://vkontakte.ru/video-245146_153408118
2 - http://vkontakte.ru/video-245146_152955505